How to connect to EDEKA via EDI
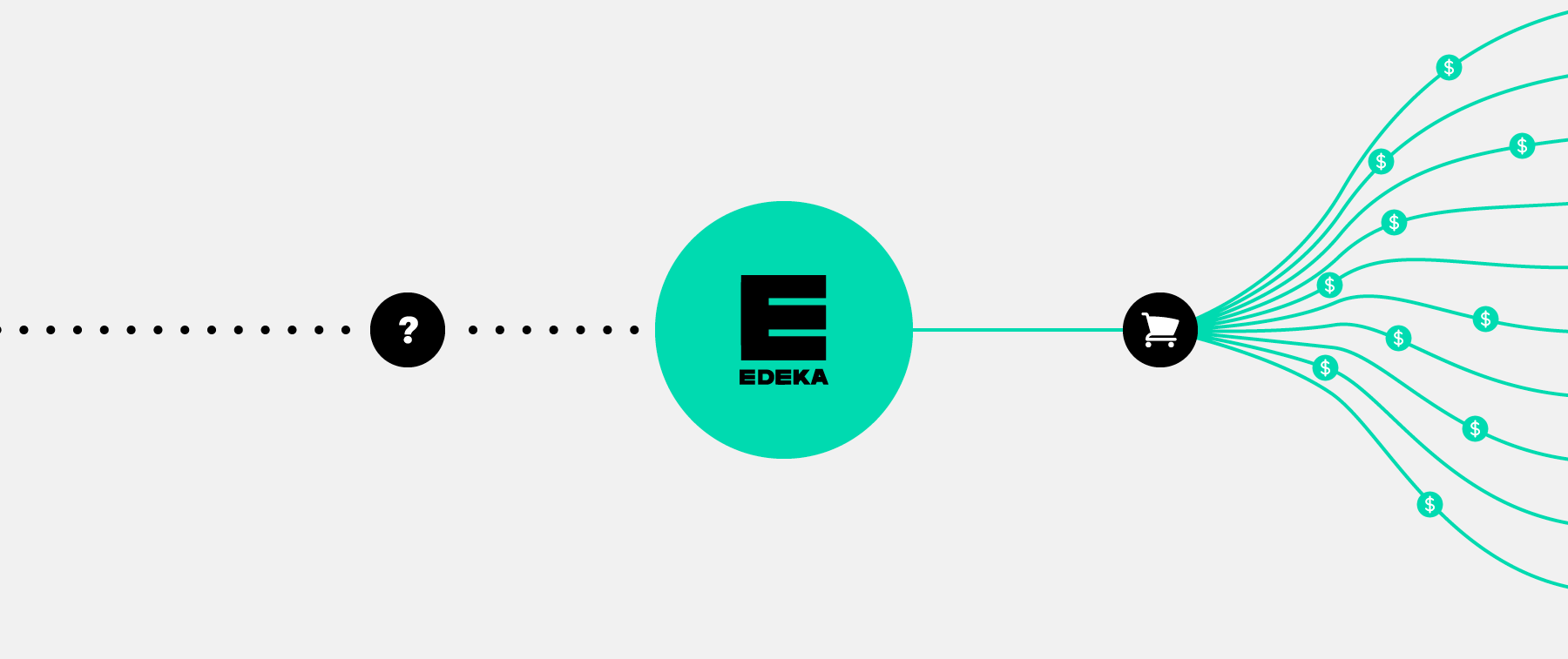
A place on the shelf at Edeka, Rewe and co. This is an important goal pursued by many companies in the food sector. They all know about the challenge to get a hard-fought place in the assortment of a big food retailer.
But when a listing at one of the 11,000 Edeka stores across Germany is within reach, a digital connection to the Edeka supplier portal becomes necessary. Nowadays, this connection is only possible through EDI and Edeka expects a smooth connection.
The Procuros Integration Hub simplifies supply chain processes between manufacturer and retail partner by integrating ERP and EDI systems.
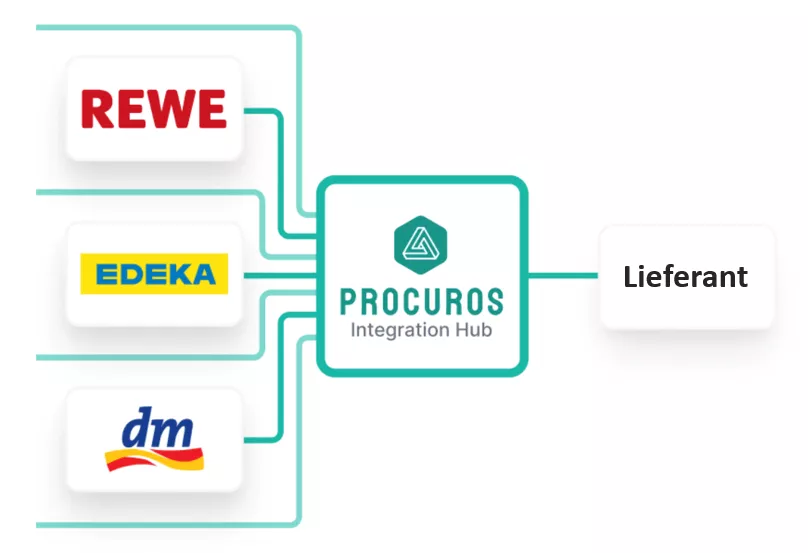
What is EDI?
EDI stands for Electronic Data Interchange. It enables the exchange of data between the ERP systems of different trading partners. A typical application is the transmission of orders, shipping notifications or invoices. In a matter of seconds, data from the Edeka merchandise system can be transferred to the supplier's own system and be processed directly. This eliminates the need for manual data entry and further time-consuming handling of these documents. Digital transmission also minimizes the likelihood of errors such as incorrectly entered quantities, prices and invoice numbers.
EDI Technology
By the way, the technology behind EDI is not entirely new: The first EDI format, ASC-X12, was introduced in North America as early as 1979. The term EDI acts as a generic term for several national and international formats.
Connection to Edeka
The Edeka Group makes use of the EDI format EDIFACT, which is one of the most popular formats created by the United Nations. The Edeka Group uses it to process orders worth over €61 billion in sales per year.
The traditional way: complex EDI mappings
The most obvious solution is the connection through classic EDI service providers. These take the existing data formats of the ERP software on both sides and create a so-called "mapping". This creates a 1:1 mapping between the data fields of both ERP systems. Mappings need to be set up for every document that you want to exchange. This includes Purchase Orders, Invoices and Shipping Notifications.
A successfully set up EDI interface then enables the following digital process chain:
- ORDER - Edeka sends a purchase order in its own EDI format, which is then converted and forwarded directly to the supplier's ERP system.
- SHIPPING NOTICE - Shipping data is converted from the supplier's ERP system into an EDI format and then transmitted to Edeka.
- INVOICE - The supplier creates an invoice in his own ERP system. The EDI service provider packages this invoice in EDI format and transfers it to Edeka.
At first glance, this does not sound particularly complicated. However, a successful EDI solution requires several complex steps that involve significant costs and time:
Mapping: a labor-intensive and manual process in which every single data field within a document must be translated into a new data format, e.g. item number, quantity, price.
Testing: After successful mapping, a test must be completed in which each document type is transmitted individually through the systems. On the customer and supplier side, the data must be checked for correctness and any errors corrected, which can be difficult since EDI doesn’t provide modern error messaging.
IT project management: The creation of an EDI connection requires accessing one of the companies' most important IT systems - the ERP. This requires close coordination between the respective IT departments on the customer and supplier side.
The path to a smooth exchange of documents is consequently far more complex than is apparent at first glance. This is also the reason for the high costs, which can often amount to thousands of euros per trading partner for individual 1:1 connections.
In view of these costs, it is particularly frustrating for many companies that this process has to be repeated for each additional trade partner. Rewe, Alnatura, Denree and co. all have different EDI interfaces with different standards and requirements.
One connection for all retail partners: The Procuros Integration Hub
An alternative solution is the Procuros Integration Hub. All order documents can be exchanged via electronic data exchange directly in the hub. The advantage over a traditional EDI connection, however is that one connection to Procuros gives you direct access to all of your trade partners at once, instead of connecting to each trade partner individually. This results in several advantages:
- Speed: Since the connection to the Procuros Integration Hub works through modern API technology, it can be connected within a few days to all common ERP systems such as WeClapp, Xentral, Odoo, Business Central, Navision, etc.
- Scalability: Once the Procuros Hub is connected, all document exchange is conducted digitally, saving hours in manual processing and data entry.
- No initial investment required: The transaction based pricing model means you only pay what you actually use, enabling you to connect to all trade partners, even when you don‘t have many orders from them yet.
The Procuros Integration Hub is based on a network architecture on which a large number of major food retailers are already connected via EDI. This eliminates the integration efforts described above for setting up new connections. The EDI integration of new retail partners can thus be implemented with just a few clicks and without time-consuming IT project management.
.webp)
Simplify your EDI connections now
Shelf space should not be compromised by a lack of digital connectivity or excessive costs. An EDI connection to Edeka and co. is not technically easy - but with the right partner at your side, it's no problem. Get in touch if you want to learn more.